Automotive wiring harness terminal crimping technical requirements and process standards
Automotive wiring harness terminal crimping technical
requirements and process standards
During the crimping process, if you change the position of the elastic piece or the terminal lip in the terminal transition area (As shown below ), Its barbs may bend excessively inward or outward, which directly affects the ability of the terminal to fully lock into the plastic housing. The crimp area is the only part of the design that is affected by the crimping process.Use Nissei IntelligentAutomatic terminal crimping machine Dedicated die-cutting blades crimp the terminal crimp area for a firm connection to the wire. Ideally, the area subject to crimp deformation occurs only in the crimp zone.
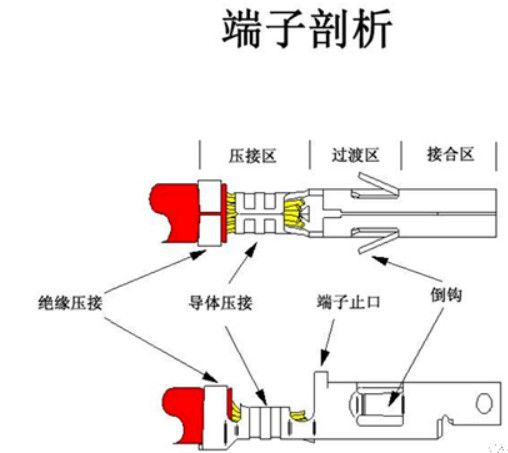
Example of a correctly executed crimp see picture B。 The insulation crimp compresses the insulation without piercing it. The core (or wire brush) protrudes beyond the front of the conductor crimp a distance at least equal to the diameter of the cable conductor. For example, #18 AWG The wire should protrude at least 0.40. Insulation and conductors are visible in the portion between the insulation and conductor crimp areas. The conductor crimp area is flared at the lead-in and tail, while the transition and splice areas remain constant before and after the crimping process.If your crimp terminal looks and B The terminals in are different, possibly due to an error in the crimping process. Here are 13 of the most common problems that can arise in the crimping process and how to avoid them.
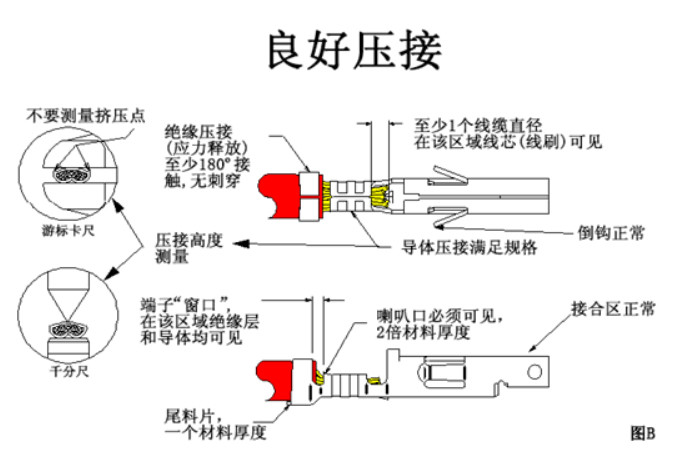
1.Crimp height too small
Crimp height refers to the cross-sectional height of the conductor crimp area after crimping, which is an important feature of a good crimp.
Too small or too large crimping height cannot maintain the specified crimping strength of the cable terminal, which will reduce the cable pulling force and rated current, and generally cause the performance of the crimping connector to degrade under abnormal working conditions. Too small crimp height can also break the wire core or break the metal in the conductor crimp area.
2.Crimp height too large
Excessive crimp height does not properly compress the wire core, causing excessive void voids in the crimp area because there is not sufficient metal-to-metal contact between the wire core and the terminal metal.
The solution to the problem is simple: adjust the conductor crimp height on the crimping machine. When working with a crimping machine, use a vernier caliper or micrometer to verify that the crimp height is within the specified range, and recheck it at the required frequency during work to maintain the correct crimp height.
Crimp height refers to the cross-sectional height of the conductor crimp area after crimping, which is an important feature of a good crimp.
Too small or too large crimping height cannot maintain the specified crimping strength of the cable terminal, which will reduce the cable pulling force and rated current, and generally cause the performance of the crimping connector to degrade under abnormal working conditions. Too small crimp height can also break the wire core or break the metal in the conductor crimp area.
2.Crimp height too large
Excessive crimp height does not properly compress the wire core, causing excessive void voids in the crimp area because there is not sufficient metal-to-metal contact between the wire core and the terminal metal.
The solution to the problem is simple: adjust the conductor crimp height on the crimping machine. When working with a crimping machine, use a vernier caliper or micrometer to verify that the crimp height is within the specified range, and recheck it at the required frequency during work to maintain the correct crimp height.
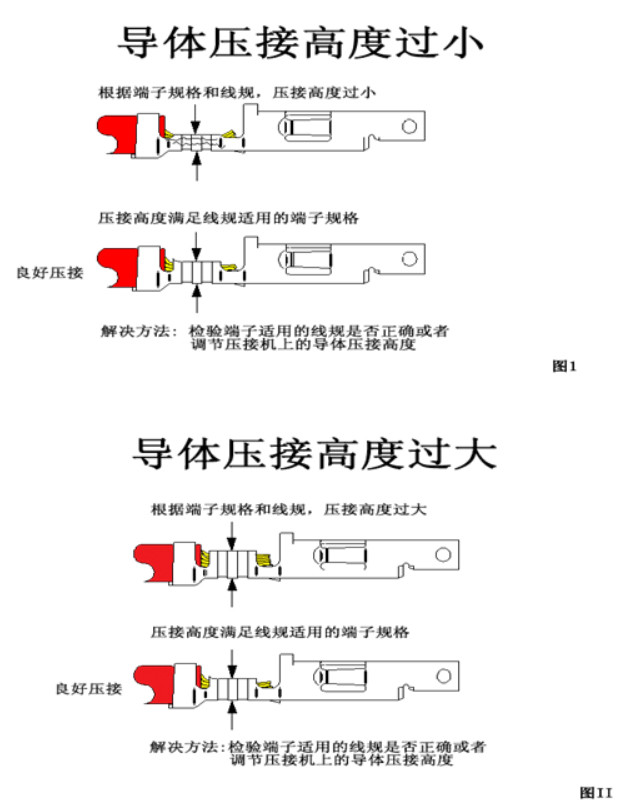
3.Insulation crimp area is too small or too large
Due to the variety of insulation types and thicknesses, connector manufacturers generally do not provide crimp heights for insulation layers. Insulation crimps provide stress relief to the conductor crimp area so that the wire core does not break when the cable is bent. A too small insulation crimping area will cause excessive stress on the metal in the insulation crimping area, weakening its stress relief function.
Most types of crimping tools can adjust the insulation crimp height independently of the conductor crimp height. Proper adjustment is such that the terminals clamp the insulation at least 180 degrees without piercing the insulation.When the outer diameter of the insulation crimping part of the terminal is close to the same as the outer diameter of the cable insulation, the best method is DT technology.
Due to the variety of insulation types and thicknesses, connector manufacturers generally do not provide crimp heights for insulation layers. Insulation crimps provide stress relief to the conductor crimp area so that the wire core does not break when the cable is bent. A too small insulation crimping area will cause excessive stress on the metal in the insulation crimping area, weakening its stress relief function.
Most types of crimping tools can adjust the insulation crimp height independently of the conductor crimp height. Proper adjustment is such that the terminals clamp the insulation at least 180 degrees without piercing the insulation.When the outer diameter of the insulation crimping part of the terminal is close to the same as the outer diameter of the cable insulation, the best method is DT technology.
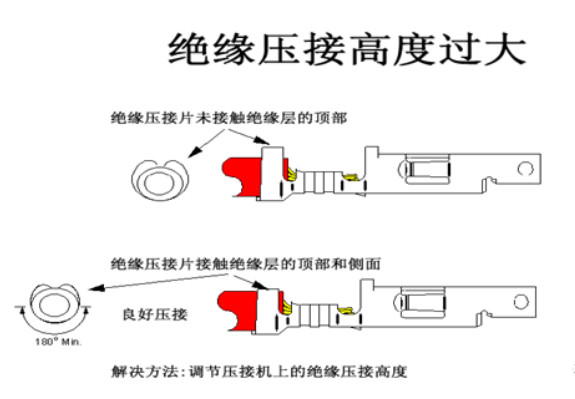
4.loose core
Loose coremaps are another common cause of crimp problems. If all cores are not completely enclosed in the conductor crimp area, the strength and current carrying capacity of the crimp will be greatly reduced. To get a good crimp, you must meet the crimp height specified by the connector manufacturer. If not all cores contribute to crimp height as well as crimp strength, the crimp will not perform as specified. Generally, loose core problems are easily fixed by simply regathering the wires into bundles and inserting them into the crimped terminals. If removing the insulation from the wire is a separate operation, the cores may be inadvertently separated during handling or bundling. Using the second stripping process and maintaining the second process to remove the insulation so that the insulation sleeve is not completely removed from the cable until it is ready to be crimped to the cable with the terminal helps to minimize the problem of loose cores.
Loose coremaps are another common cause of crimp problems. If all cores are not completely enclosed in the conductor crimp area, the strength and current carrying capacity of the crimp will be greatly reduced. To get a good crimp, you must meet the crimp height specified by the connector manufacturer. If not all cores contribute to crimp height as well as crimp strength, the crimp will not perform as specified. Generally, loose core problems are easily fixed by simply regathering the wires into bundles and inserting them into the crimped terminals. If removing the insulation from the wire is a separate operation, the cores may be inadvertently separated during handling or bundling. Using the second stripping process and maintaining the second process to remove the insulation so that the insulation sleeve is not completely removed from the cable until it is ready to be crimped to the cable with the terminal helps to minimize the problem of loose cores.
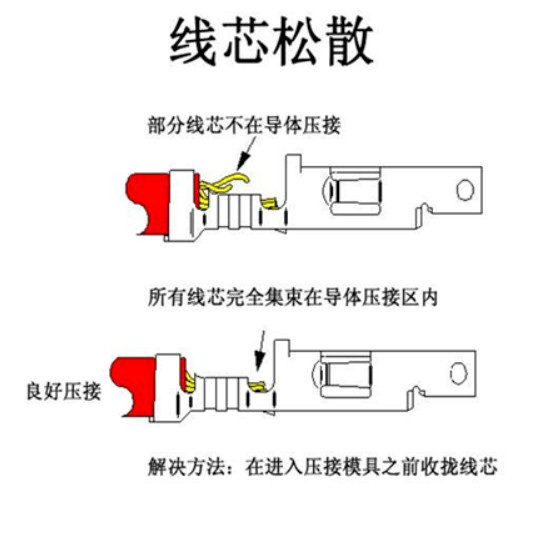
5.Stripping length is too short
If the stripped length is too short, or if the wire is not fully inserted into the conductor crimp area, the termination may not be able to achieve the specified pullout force because there is less metal-to-metal contact between the wire and the terminal (as the picture shows ),The stripped length of the cable is too short (note that the insulation is in the correct position ), Protrusion beyond the front of the conductor crimp area does not allow for the required OD of one cable. The solution is simple: increase the stripping length of the stripping device to the specified value for that terminal.
If the stripped length is too short, or if the wire is not fully inserted into the conductor crimp area, the termination may not be able to achieve the specified pullout force because there is less metal-to-metal contact between the wire and the terminal (as the picture shows ),The stripped length of the cable is too short (note that the insulation is in the correct position ), Protrusion beyond the front of the conductor crimp area does not allow for the required OD of one cable. The solution is simple: increase the stripping length of the stripping device to the specified value for that terminal.
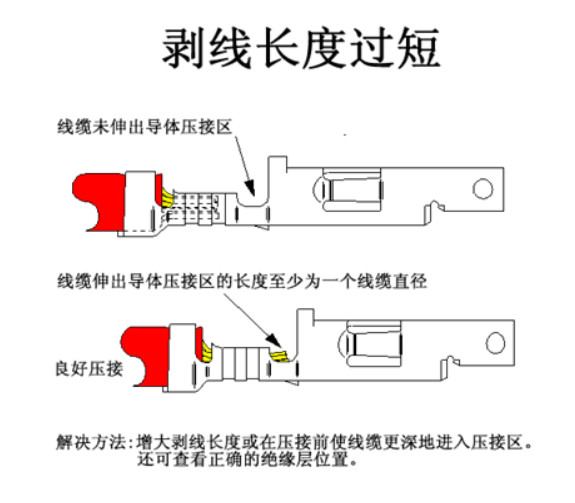
6.Cable inserted too deep
Another crimp problem associated with too short a strip length occurs when the wire is inserted too far into the crimp area. As shown, the insulation is inserted too far forward into the insulation crimp area, and the conductor sticks out into the over-concentrated area. In practice, this can cause three failure modes. Two of these are due to reduced metal-to-metal contact in the conductor crimp area, which reduces current rating and cable pull-out force. The connection between metal and plastic is not as strong as that of metal, and it does not conduct electricity.
A third failure mode can occur when the connectors are mated. If the wire protrudes too far into the transition, the tips of the pin terminals hit the upper cymbal, which may prevent the connector from fully seating, or may cause the pin or socket terminals to bend. This situation is called two-terminal collision three.
In extreme cases, even though the terminals are fully seated within the housing, they can be pushed out of the back of the housing. To resolve this issue, make sure the wire is not inserted into the crimper past the wire stop on the crimper with excessive force, or adjust the position of the cable stop to properly axially position the stripped cables.
Another crimp problem associated with too short a strip length occurs when the wire is inserted too far into the crimp area. As shown, the insulation is inserted too far forward into the insulation crimp area, and the conductor sticks out into the over-concentrated area. In practice, this can cause three failure modes. Two of these are due to reduced metal-to-metal contact in the conductor crimp area, which reduces current rating and cable pull-out force. The connection between metal and plastic is not as strong as that of metal, and it does not conduct electricity.
A third failure mode can occur when the connectors are mated. If the wire protrudes too far into the transition, the tips of the pin terminals hit the upper cymbal, which may prevent the connector from fully seating, or may cause the pin or socket terminals to bend. This situation is called two-terminal collision three.
In extreme cases, even though the terminals are fully seated within the housing, they can be pushed out of the back of the housing. To resolve this issue, make sure the wire is not inserted into the crimper past the wire stop on the crimper with excessive force, or adjust the position of the cable stop to properly axially position the stripped cables.
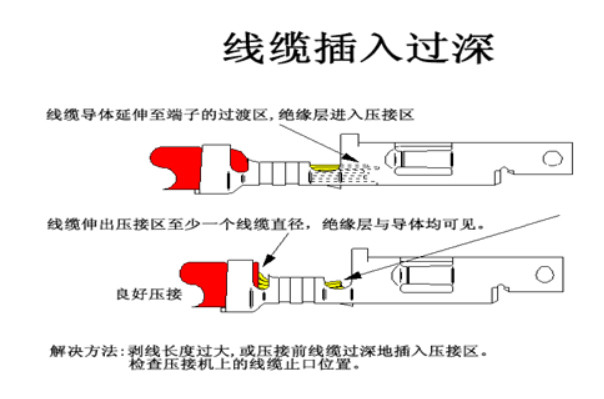
7.excessive bendingterminal
It is also vividly called banana crimping, because the crimping terminal is in the shape of a banana. This makes it difficult to insert the terminals into the housing, possibly causing terminal bumps. This problem is easily solved by adjusting the position of the limit pin on the crimping machine. This small pin is located in the crimping machine and contacts the mating area of the terminal when the crimping area is crimped on the wire. During the crimping process, the metal on one end of the terminal (in the crimping area) moves. Such a large force tends to force the front of the terminal upward unless restrained by a suitable restraining pin.
It is also vividly called banana crimping, because the crimping terminal is in the shape of a banana. This makes it difficult to insert the terminals into the housing, possibly causing terminal bumps. This problem is easily solved by adjusting the position of the limit pin on the crimping machine. This small pin is located in the crimping machine and contacts the mating area of the terminal when the crimping area is crimped on the wire. During the crimping process, the metal on one end of the terminal (in the crimping area) moves. Such a large force tends to force the front of the terminal upward unless restrained by a suitable restraining pin.
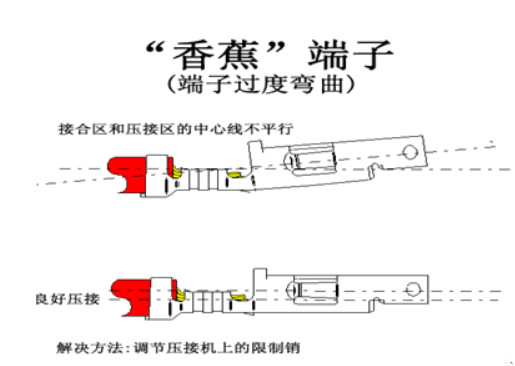
8.Crimp too far forward
One of the more obvious crimping problems is localized damage to the transition area. In the terminal shown, the vertical protrusion is a design feature called a terminal lip. Its function is to prevent the terminals from being inserted too far into the housing. If the lip is completely destroyed, the actual terminal will be pushed all the way through the housing.
The solution is relatively simple. This problem is caused by incorrect positioning of the terminals and the metal strip (the metal strip the terminals are attached to when you receive it from the manufacturer) relative to the crimping machine. Simply loosen the base plate of the interchangeable tool and realign the crimper and the problem is solved.
One of the more obvious crimping problems is localized damage to the transition area. In the terminal shown, the vertical protrusion is a design feature called a terminal lip. Its function is to prevent the terminals from being inserted too far into the housing. If the lip is completely destroyed, the actual terminal will be pushed all the way through the housing.
The solution is relatively simple. This problem is caused by incorrect positioning of the terminals and the metal strip (the metal strip the terminals are attached to when you receive it from the manufacturer) relative to the crimping machine. Simply loosen the base plate of the interchangeable tool and realign the crimper and the problem is solved.
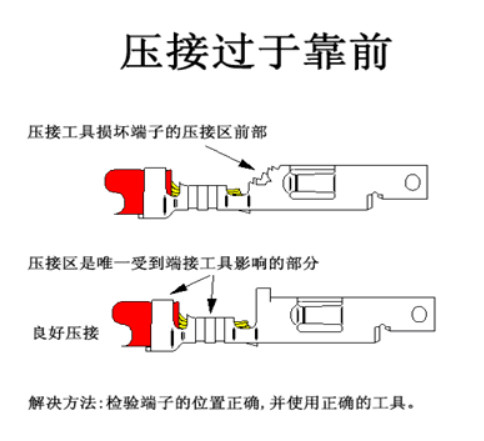
9.bell mouthtoo small
The correct size of the flare is approximately 2 times the thickness of the terminal material. It essentially affects the performance of the terminal. If the bell mouth is missing, or it is less than the thickness of the terminal material, there is a danger of cutting the core. Retaining fewer cores reduces termination strength. To correct this problem, verify that the punch and seat on the crimping equipment are properly aligned.
The correct size of the flare is approximately 2 times the thickness of the terminal material. It essentially affects the performance of the terminal. If the bell mouth is missing, or it is less than the thickness of the terminal material, there is a danger of cutting the core. Retaining fewer cores reduces termination strength. To correct this problem, verify that the punch and seat on the crimping equipment are properly aligned.
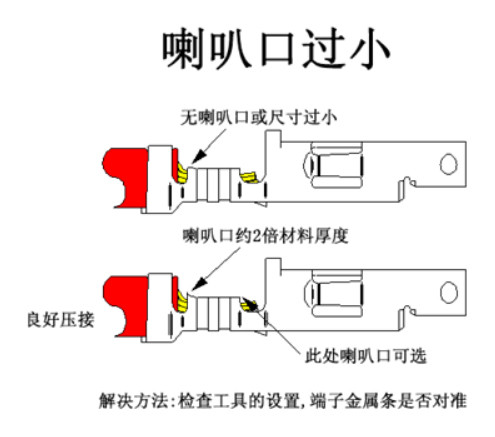
11. tail too long
Tails are trimmed from the terminal during the crimping process. Problems can arise if the remaining tail is too long. When the terminals are inserted into the housing, excessively long metal tails can protrude to the rear of the connector, causing arcing between adjacent contacts of the connector when higher voltages are applied. If the tail material on the front of the terminal is too long, it can interfere with the mating of the connector and cause "terminal bumping".
Nissei Intelligence focuses on wire harness automation processing equipment solutions and R & D and manufacturing, The solution is relatively simple. Adjust the feed plate on the press so that the terminal is properly centered in the press. Another sign that the terminal is not properly centered is that the flare is not properly formed. This occurs because the bell mouth has a spatial relationship to the tooling of the tail.
12. barb bend
Although barb bending is not necessarily the result of an incorrect crimping process, connectors can still fail. The barbs may be bent excessively inward or outward, which affects the ability of the terminal to fully lock into the plastic housing. Barb damage can be caused by the friction wheels on the crimper's shaft holder being too tight when the terminal is unwound from the reel, or by handling the terminal after it has been crimped onto the wire. Typically terminated cables are bundled and stored or shipped to another location in the factory. The barbs may also bend during the bundling process, or as each terminated wire is removed from the harness.
Tails are trimmed from the terminal during the crimping process. Problems can arise if the remaining tail is too long. When the terminals are inserted into the housing, excessively long metal tails can protrude to the rear of the connector, causing arcing between adjacent contacts of the connector when higher voltages are applied. If the tail material on the front of the terminal is too long, it can interfere with the mating of the connector and cause "terminal bumping".
Nissei Intelligence focuses on wire harness automation processing equipment solutions and R & D and manufacturing, The solution is relatively simple. Adjust the feed plate on the press so that the terminal is properly centered in the press. Another sign that the terminal is not properly centered is that the flare is not properly formed. This occurs because the bell mouth has a spatial relationship to the tooling of the tail.
12. barb bend
Although barb bending is not necessarily the result of an incorrect crimping process, connectors can still fail. The barbs may be bent excessively inward or outward, which affects the ability of the terminal to fully lock into the plastic housing. Barb damage can be caused by the friction wheels on the crimper's shaft holder being too tight when the terminal is unwound from the reel, or by handling the terminal after it has been crimped onto the wire. Typically terminated cables are bundled and stored or shipped to another location in the factory. The barbs may also bend during the bundling process, or as each terminated wire is removed from the harness.